Love Thy Roof
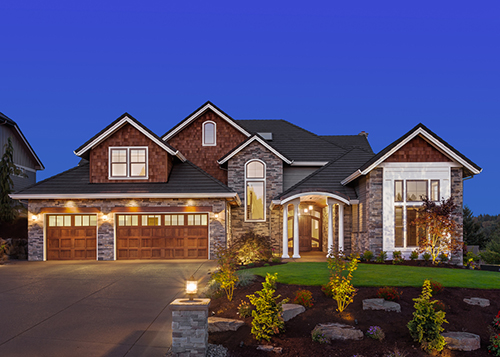
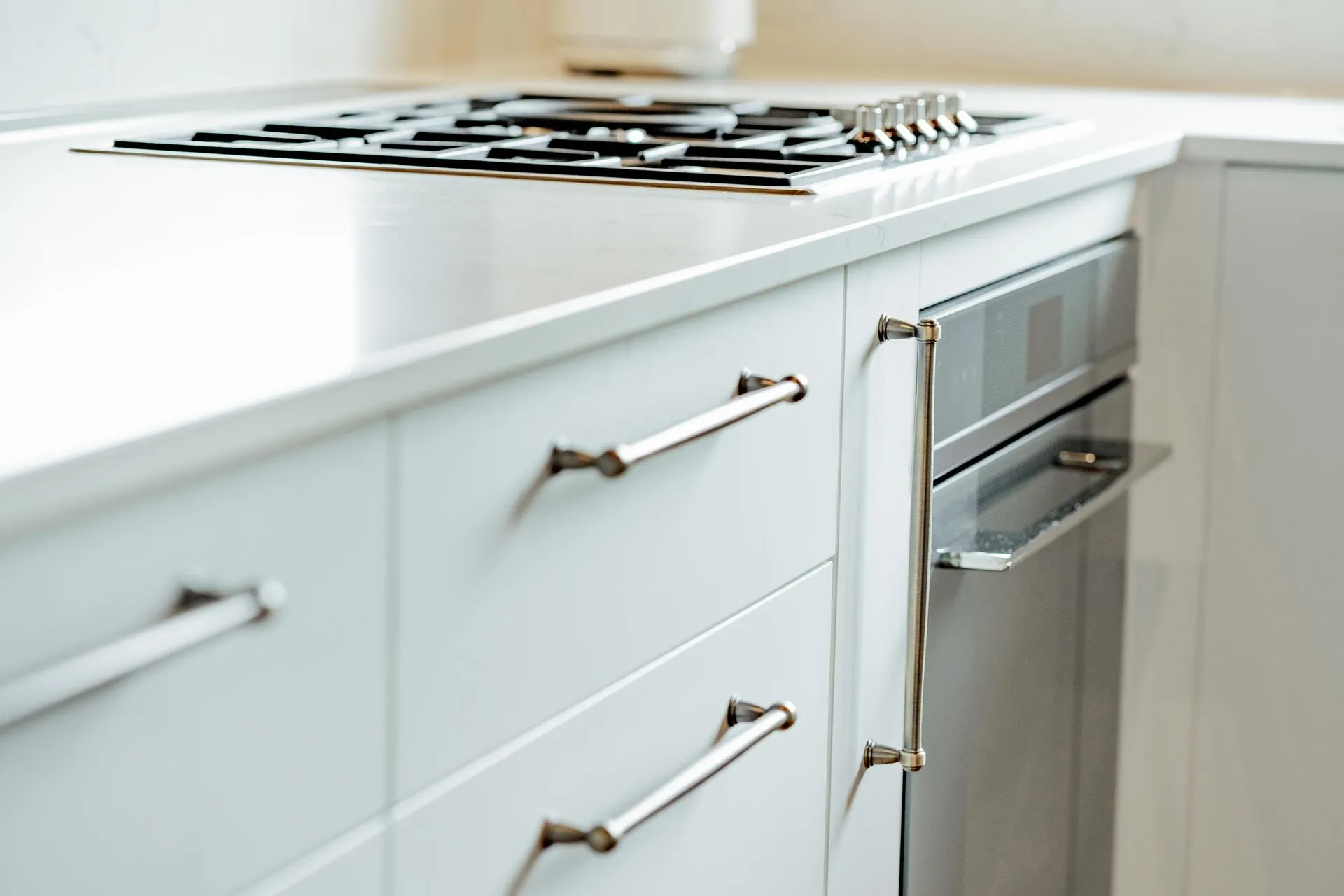
Love Thy Roof
by | May 5, 2020 | Maintenance
For many of us the roof is out of sight and out of mind. This is fine as long as we understand the characteristics of our roofs, inspect and carry out maintenance at least once a year and keep good records of installers, repairs and warranties.
KNOW THY ROOF
Roof cladding varies in cost, upkeep, appearance and durability. Your roof affair should not stop there, however, as factors such as weight and noise need consideration. It is also sensible to understand how your roof would handle a large earthquake or violent storm.
According to NZ Metal Roof Manufacturers (NZMRM), over 70% of housing in New Zealand is clad with metal roofs of long run or metal tiles. Steel & Tube Roofing Products commercial manager Rod Newbold, says when it comes to steel roofing the corrugated look is still number one in New Zealand.
“It is a classic,” Newbold says. “If you look at “House of the Year” every category will have a corrugated steel roof.”
The lightweight and resilient qualities of steel roofing have major benefits. However they can be noisy, for instance in heavy downpours, and after violent storms sheets of corrugated iron can sometimes be seen decorating a neighbour’s yard. Concrete tiles on the other hand diffuse noise and their weight means they are unlikely to blow away.
Following the Christchurch ‘quakes Stuart Thomson, in an NZMRM article, writes that metal roofs fare better than heavy tile roofs. “The diaphragm action of the roof cladding literally can hold the building up as illustrated by this picture of the 160 year old Dean Homestead at Home Bush,” Thomson says.
A 2010 report commissioned by BRANZ and written by J Fung (Study Report 248), on the life cycle costs of common roof claddings used in New Zealand, concludes the most cost-effective roof cladding systems are corrugated steel, concrete and clay tiles.
The latter two have longer life spans than other claddings. Also, depending on the environmental conditions, concrete and clay tiles require little maintenance (repointing every 20-25 years and painting every 25-30 years), whereas prepainted steel or metal tiles require painting every 7-10 years.
The estimated lifespan of different claddings is shown in the table below.
Cladding System Estimated life
Concrete Tiles 90
Aluminium .90 mm 80
Aluminium .70 mm 70
Clay Tiles 60
Prepainted Steel 0.40 mm 50
Prepainted Steel 0.55mm 50
Metal Tiles 50
Unpainted Steel 0.40 mm 25
Unpainted Steel 0.55 mm 25
Butyl Membrane 25
Asphalt Tiles 20
Structural framing requirements for a lightweight metal roof are less than for a heavy weight roof (eg concrete tiles, slate) which according to a NZMRM report by Mike Flooks can deliver savings of around $3,000 or $9.95 per square metre for a typical single storey house.
CARE FOR THY ROOF
There is, alas, no such thing as a maintenance free roof. Your roof is exposed not only to the elements but also to air pollutants and chemicals, bird deposits and wind-blown debris or fallen leaves. Lichen or algae growth can degrade the cladding and different rates of expansion or contraction between the roof and the structure can open up fastenings or cause movement of tiles.
The product manufacturer of your roofing material will have guidelines about maintaining their product. It is essential that these are followed not only to preserve the roof but also to ensure any warranty is not voided.
Your roof should be inspected at least once a year to ascertain its condition and necessary steps should be taken to rectify any problems.
CLEAN THE GUTTER
When gutters or downpipes are blocked, a build up of water overflows back into your roof. Cleaning the gutters is the most basic step in roof care. Remove all debris out of the gutters and check they are draining properly. Also, check debris is not building up in any gaps between the spouting and the fascia or walls. If leaf fall is in great volume, it may be necessary to clean gutters several times a year. Better still, remove any surrounding branches that overhang the roof or give rise to leaf fall. Refasten or replace non-functioning gutters.
Structures such as chimneys, skylights or plumbing vents are main sources of leaks and can also divert the natural water flow. Water and debris can be trapped around them and flashings or seals may deteriorate faster than the roof material. Step and counter-flashings are necessary to prevent water entering around these spots.
Check where the roof terminates around the walls and under the eaves.
Drip-edge flashings protect the edges of roof sheathing from water penetration caused by driving rains. A drip-edge also helps to keep out insects and other pests. Ensure the drip-edge is intact and no corrosion appears on the underside of the roof where it overhangs the walls.
CHECK ALL ROOF FIXINGS
Nails or screws that hold the roof in place should be checked for tightness and to ensure there is no degradation of the metal.
Look for blooming around roof fasteners. “Technology for fasteners has not kept pace with roof technology” Rod Newbold says. The roof may be sacrificing itself for the screw.
Maintain To Profit director Dean Larritt, says old timber houses, particularly those on piles, expand and contract with heat and cold. This causes the roofing material, particularly corrugated iron, to move. The old lead head nails wiggle around, opening up holes through which a surprising quantity of water is able to happily flow onto unsuspecting heads below.
“If the roof is in good condition this is simple and cheap to fix merely by replacing the nails with new fixings,” Larritt says.
CHECK CLADDING
The simple act of inspecting your roof can cause damage so be careful where you putyour feet. Walk only along the fastener line on steel roofs or the strip where the tiles overlap on a tile roof.
Steel sheets can dent and older tiles are easily cracked or dislodged, needing replacement or repair. Any corrosion of metal cladding needs to be treated to halt its advance. Address the cause of the rust. Sometimes when corrosion occurs between for example, flashings and roof sheeting, materials consisting of metals that compromise one another may have been installed.
On a tile roof, blocked drainage channels under individual tiles should be cleared.
CHECK ROOF CAVITY
It is also important to check inside the roof cavity. “Excessive internal moisture can lead to failure of the roof and rotting of framing,” Newbold says. “Look out for wet insulation or drip marks or even mould on purlins.” If moisture is detected the first line of defence is to introduce ventilation into the attic space.
CLEAN VALLEYS AND WASH ROOF
Valleys in the roof deal with large volumes of water so it is important they are not allowed to get blocked. Larritt advises use of a degreasing and cleaning agent when washing the roof. “Remember to disconnect downpipes from the drinking water tank if the home is on tank water,” he says. Lichen growth should be treated appropriately. Take particular care to wash areas which do not get naturally washed by rain.
You may need to repaint or resurface if necessary.
If the roof needs repainting wait at least one month after applying lichen treatment, Larritt says. Wash off all residues and apply two coats of acrylic roof paint for a pre-painted steel roof. For unpainted steel it is essential to use a galvanised iron primer such as Resene Galvo One before applying the two coats of acrylic paint. For roofs within 500 metres of the sea Resene recommends a second coat of primer before applying the top coats.
LEAKS
Larritt advises to always start from the roof down when inspecting a house. “It is something I learnt as a kid washing the car with my father,” he quips.
“If there are issues inside the house, for instance stains on walls, the logical place to start is the roof.”
Larritt says it’s rare the roof itself is actually leaking. Usually the problem will be where fasteners or a structure like a chimney penetrates the roof or where the roof terminates or changes direction at walls or valleys.
Leaks can be very deceiving and water can travel a long way along invisible channels to where it finally starts seeping through the ceiling and down walls.
HEALTH AND SAFETY
Annual roof inspection is important, but it is even more important to carry it out safely. Around 4,000 Kiwis annually sustain serious injuries falling from ladders on private property.
Firstly, ensure someone knows you are climbing onto the roof. Preferably, they should be watching you and holding the ladder steady when climbing or descending or working on it.
It is important to use a ladder in good condition, of correct height and to know its weight capacity.
Call the professionals if the problem is serious or your roof is too high or steep to safely carry out maintenance yourself.
Larritt cautions that the Health and Safety at Work Act, due to come into force in April, 2016, places greater onus on homeowners to ensure contractors working on their property have health and safety policies and operate safely.
KEEP GOOD RECORDS
When purchasing a house, ask the vendor for warranties and records of the installer and any repairs to the roof. This could prove invaluable if post-purchase issues arise.
Always keep good records if you build a house yourself or have work carried out on your roof. And ask for a warranty. “I don’t know of a roofing company that doesn’t warrant repairs it carries out,” Larritt says.
As roofing is part of the weathertightness of a building, it is considered as restricted building work (RBW) and must be carried out by a licensed building practitioner (LBP). Roofers, much the same as builders, must be registered and this has legal implications for a vendor if there are any problems with a newly installed or repaired roof, not installed by an LBP.
SHOW YOUR TRUE METAL
All steel roofing has a metallic coating on both sides of the sheet which protects against rusting. This is underneath and separate from any paint which imparts colour to the product.
Two types of metallic coatings are used:
Galvanised: This is 100% zinc in various thicknesses depending upon the product usage.
Galvalume or Zincalume: A mixture of aluminium and zinc. (55% by volume aluminium)
Metallic coatings “sacrifice” themselves to protect the iron (Fe) in steel from oxidation when exposed to the air and moisture is present. Zinc is a more “active” metal than iron so it oxidises first and forms a protective barrier – zinc oxide, before the iron (Fe) in the steel can become Ferric Oxide (rust).
Order of sacrifice:
Zinc/aluminium.
Steel.
Lead copper.
Stainless steel.
The metals higher on the list will sacrifice themselves for metals lower on the list.
This article is reprinted from NZ Property Investor magazine October 2015 issue.
Renovate with Us
MTP Renovations are one of New Zealand’s leading renovating specialists, we have helped hundreds of satisfied clients - now its your turn!
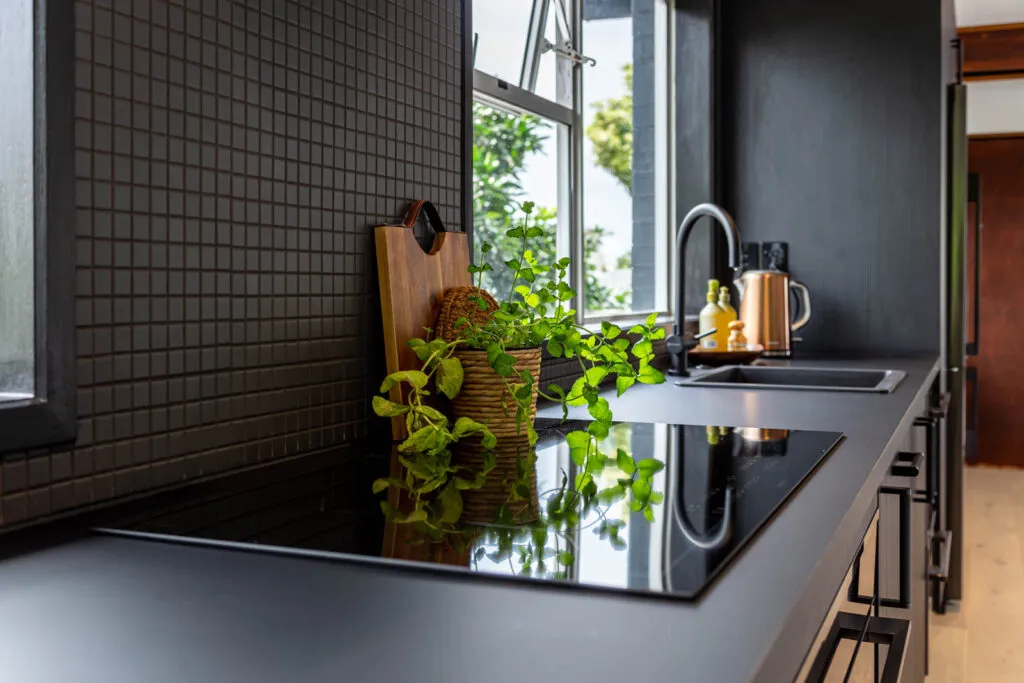